Produire plus en réduisant sa facture énergétique ? C’est possible et les solutions existent !
parLa volatilité des coûts de l’énergie touche tous les secteurs d’activité, et la mécanique ne fait guère exception. Entre baisses des marges et pertes de marché face à des concurrents produisant hors d’Europe (là où l’énergie est souvent moins chère), les ateliers d’usinage doivent redoubler d’efforts, d’inventivité mais aussi d’investissements pour réduire leurs consommations. Heureusement, des solutions existent, et ce à toutes étapes du process d’usinage pour gagner en sobriété.
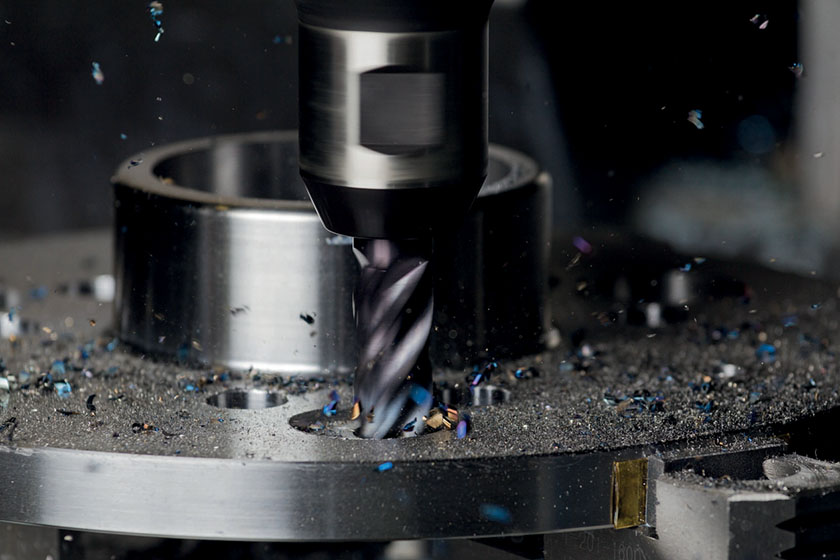
La Cop28 vient de fermer ses portes avec quelques nouvelles avancées (malgré le bras de fer persistant avec les pays de l’Opep) afin de préserver un peu plus la planète du réchauffement climatique. Et il est grand temps… En 2021, l’industrie était responsable de 19% de la consommation d’énergie primaire de la France, selon le Commissariat général au développement durable. Autre chiffre significatif, en 2020, le groupe de réflexion français La Fabrique Écologique a estimé que l’industrie était responsable de 32% de la pollution de l’air en France.
Mais du côté des usineurs, même si la conscience environnementale fait son chemin, l’heure est plutôt aux économies d’énergie. En deux mots, « produire mieux ». Une nouvelle manière de concevoir l’usinage qui procure un double avantage, celui de fabriquer de manière plus économique (et de gagner en marge) tout en optimisant l’utilisation de son outil de production afin d’allonger sa durée de vie.
Mais comment faire concrètement ?
Plusieurs solutions existent sur le marché. Avant tout, des initiatives – telles que le guide dédié à la maîtrise de l’énergie dans l’atelier d’usinage, co-écrit par le Cetim et l’Ademe (cf. pages suivantes) – ont le mérite d’exister tout comme les nombreux événements tels que des portes ouvertes chez les carburiers, fabricants de machines-outils, de lubrifiants et d’instruments de métrologie, ou encore des éditeurs de logiciels (CFAO…) qui mettent de plus en plus l’accent sur les économies d’énergies lors des démonstrations d’usinage et autres conférences techniques. Ensuite, ces mêmes fournisseurs de solutions s’engagent de plus en plus dans la brèche de l’efficacité énergétique, tant au niveau de la production de leurs propres produits – à travers des politiques RSE de plus en plus engagées – que dans leur utilisation. Objectif ? Proposer au marché de la mécanique des solutions leur permettant – en plus de gagner en productivité et en performances d’usinage – de gagner en rendement et ainsi d’économiser de l’énergie (et de l’argent).
Dans ce contexte, il est de plus en plus fréquent de voir sur les machines-outils des technologies de contrôle avancées telles que les automates programmables, les variateurs de vitesse et les capteurs intelligents afin d’optimiser leur consommation d’énergie. Sur l’équipement, les compteurs d’énergie permettent par exemple de mesurer la consommation afin d’identifier les zones de gaspillage d’énergie et de prendre les mesures qui s’imposent. De même, les capteurs de température et d’humidité donnent la possibilité de surveiller les conditions environnementales dans les installations et ainsi d’optimiser les processus de production afin de minimiser les pertes d’énergie. Autre solution en vogue, les systèmes de surveillance en temps réel de la consommation d’énergie qui, en étant connectés à des logiciels d’analyse de données, aident à identifier les zones de gaspillage et optimiser les processus de production.
L’automatisation peut également contribuer à réduire la consommation d’énergie en minimisant les pertes liées aux processus manuels et en optimisant les temps d’utilisation des machines.
Enfin, il est essentiel de sensibiliser l’ensemble du personnel (quel que soit le service afin d’impliquer tout le monde autour d’un même objectif) aux bonnes pratiques d’économie d’énergie et proposer des formations sur les techniques d’optimisation énergétique. Il faut encourager les employés à adopter des comportements écoresponsables, tels que l’extinction des machines et des lumières lorsqu’ils ne sont pas utilisés.
De plus en plus de solutions sur le marché
Les constructeurs de machines-outils se mettent au vert. La consommation d’une machine étant le premier poste de dépense (avant l’acquisition de l’équipement), il est d’ores et déjà pertinent d’optimiser son utilisation, sans pour autant investir dans des machines dernier cri. Concernant les machines neuves et récentes, les constructeurs lancent des modèles équipés de systèmes de récupération d’énergie et d’utilisation de chaleur résiduelle. Au moment où la broche décélère, l’énergie est renvoyée dans le réseau d’électricité. Dans la robotique aussi, les unités de condensateur visant à récupérer l’énergie du freinage sont présentes, qu’il s’agisse de robots de soudage ou de robots de chargement.
Il en est de même pour les équipements venant alimenter la machine, comme les compresseurs à air comprimé ou les pompes. Outre le fait de ne pas « succomber » à la tentation de surdimensionner son équipement et d’utiliser des variateurs de vitesse, des instruments de mesure permettent aujourd’hui de surveiller sa consommation en détectant les fuites via des capteurs à ultrason.
Installer des instruments de mesure et de monitoring sur sa machine, grâce à différents types de capteurs (de vibration, de température, d’humidité, de tension ou de pression selon les équipements de production à surveiller) se révèle intéressant, d’autant qu’aujourd’hui ces systèmes peuvent être connectés entre eux et remonter des informations en temps réel vers un logiciel de Manufacturing Execution System (MES). Le recueil des données aide à mieux les analyser et surveiller (grâce à des alertes) l’état de santé de la machine mais aussi sa consommation énergétique. Plusieurs types de MES existent, du système complet à des solutions en mode SaaS. Il sera ainsi plus simple de suivre la consommation d’énergie et identifier les domaines où des améliorations peuvent être apportées.
Toujours du côté des logiciels, mais cette fois des outils appliqués à l’enlèvement de matière tels que la CFAO, il est possible aussi de gagner en consommation d’énergie. C’est le cas notamment de l’usinage dynamique qui permet d’augmenter la durée de vie des outils coupants et ainsi de réduire leur consommation. En optimisant les parcours d’outils et en réduisant les temps d’usinage, on gagne en économie d’énergie. Enfin, c’est sans compter les outils de simulation d’usinage et l’apport des jumeaux numériques. L’objectif ? Modéliser l’ensemble du process afin d’éviter le gaspillage de matière et des opérations d’usinage menant à une hausse des consommations de la machine. Enfin, le jumeau numérique offre plus de chances d’obtenir une pièce juste, du premier coup.
Agir directement sur le process d’usinage
Côté mécanique cette fois, les fabricants s’impliquent eux aussi dans l’efficacité énergétique et la réduction de l’empreinte environnementale, à l’exemple de certains carburiers qui étudient les meilleures méthodes d’usinage, à la fois à partir de matériaux très résistants (comme le cas d’un équipementier automobile qui s’est mis aux plaquettes CBN pour réduire ses temps de cycle – donc sa consommation d’énergie – et les casses d’outils tout en n’ayant moins d’arêtes de coupe)… ou encore ce carburier qui propose des plaquettes de plus petites tailles pour limiter le nombre de déchets en usinage. Il est aussi possible de réduire ses temps de cycle en augmentant le nombre d’arêtes de coupe mais aussi de se tourner vers les fraises à segment de cercle qui, avec leur grand rayon de profil, permettent de réduire le nombre de passes. Tout est donc une question de calcul et d’essai, et donc une culture à adopter dans l’atelier pour toujours aller chercher la technologie qui offrira la meilleure solution et répondra au besoin.
Du côté des lubrifiants aussi, les choses bougent. Longtemps pointées du doigt comme étant sales et toxiques, les huiles de coupe font désormais pleinement partie d’une démarche d’efficacité énergétique d’un atelier d’usinage. S’orienter vers des fabricants d’huiles déjà très investis dans des formulations plus respectueuses de l’environnement, c’est se diriger vers des produits mieux adaptés aux process et nécessitant moins de maintenance. En matière de coûts d’utilisation, ces produits à la durée de vie élevée impliquent aussi moins de vidanges et moins de retraitement de l’huile. Celle-ci est également plus fluide, moins volatile et permet ainsi d’allonger la durée de vie de la broche. Cependant, changer de lubrifiant ne suffit pas. Il est important aussi de s’équiper d’un bon système de filtration et de procéder au moins une fois par an à une analyse de l’huile tout en veillant à l’entretien du système d’aspiration.
Ces économies d’énergie forment un ensemble connecté, à l’image du process industriel. Intervenir là-dessus n’est pas simple, mais en étant bien accompagné, on verra de très rapides retours sur investissement.
Olivier Guillon
EQUIP PROD – N°148 – Décembre 2023