Mesurer automatiquement l’épaisseur d’une pièce directement dans la machine, un enjeu pour l’aéronautique !
HEXAGON MANUFACTURING INTELLIGENCE / M&H
parL’épaisseur restante d‘une pièce après usinage est une information de plus en plus importante. Grâce à un nouveau palpeur à ultrasons, Hexagon permet de mesurer et enregistrer ce critère de manière fiable et répétée, directement dans la machine. Une innovation majeure lorsqu’on pense que la mesure d’épaisseur de paroi avant la finition deviendra la norme pour de nombreuses pièces, en particulier dans l’industrie aérospatiale.
L’optimisation du poids, les échanges thermiques, le refroidissement homogène, les garanties de résistance, entre autres, sont des critères de plus en plus prépondérants dans la fabrication de pièces et de composants. La prise en compte de ces critères pendant leur fabrication nécessite des points de contrôle de plus en plus nombreux et de les enregistrer. À titre d’exemple, pour minimiser leur poids, les pièces de grande surface pour l’industrie aéronautique sont conçues en nid d’abeille. Ces composants, d’une taille allant jusqu’à 4x10m, sont façonnés d’un côté avec des courbures légèrement sphériques, tandis que de nombreuses poches en forme de nid d’abeille sont fraisées de l’autre côté. Il n’est pas rare de trouver des pièces ayant jusqu’à 160 « Pockets » de ce type. En raison de la résistance requise et du poids sévèrement contrôlé, il est important que l’épaisseur restante de matière fraisée au niveau des poches soit maîtrisée avec précision.
Dans le processus de fabrication traditionnel, l’épaisseur de tous les nids d’abeilles des premières pièces est manuellement contrôlée par ultrasons après usinage. Occasionnellement, cette inspection a lieu à la fois avant et après la finition. Il s’agit généralement de deux contrôleurs qui travaillent plusieurs heures. On calcule qu’il y a au moins 15 secondes par point de mesure, ce qui correspond à 80 minutes par contrôleur pour 160 nids d’abeilles mesurées en deux points. Malgré un personnel spécialement formé, des erreurs et des incertitudes de manipulation difficiles à déceler se produisent régulièrement.
Les imprécisions de mesure, les ruptures de transmissions et les coupures sur les arêtes vives ne sont pas rares. De plus, les sondes à ultrasons manuelles ont besoin d’un fluide de contact afin de pouvoir introduire les ondes sonores dans la pièce. Dans la plupart des cas, la deuxième pièce est en attente d’usinage car elle doit être corrigée en fonction des résultats de mesure de la première pièce.
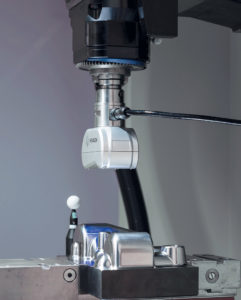
› Avec son système breveté de mesure par ultrasons dans la machine-outil, Hexagon
ouvre de nouvelles voies dans la mesure automatique des épaisseurs de paroi
Une même base pour plusieurs variantes
Depuis plus de quinze ans, m&h ne cesse d’innover dans les techniques de mesure sur machines-outils. De nombreux clients témoignent ainsi de son leadership technique sur le marché dans diverses applications, sans oublier les nombreux brevets de produits et de procédés. Suite aux demandes de ses clients, Hexagon a résolu le problème technique décrit ci-dessus et a intégré la technologie ultrason dans sa gamme de palpeurs. Le corps de base du palpeur repose sur la même technologie de transmission radio sécurisée que celle qui est déjà installée dans de nombreuses machines-outils. Cette technologie en constante évolution intègre aujourd’hui la communication bidirectionnelle et la possibilité d’utiliser plusieurs palpeurs indépendamment les uns des autres, comme par exemple dans les machines multibroches.
Depuis des années, Hexagon mise sur la modularité de ses palpeurs pièce. Différents mécanismes de mesure peuvent ainsi être utilisés dans le seul et même corps du palpeur en acier inoxydable et peuvent être échangés à tout moment. Avec la même base, il est possible d’utiliser soit un système de mesure tripode traditionnel, un système hémisphérique pour les machines sans orientation broche, un capteur laser de très haute précision un capteur de température pour la prise en compte du comportement thermique de la pièce, ou encore, depuis peu, un système de mesure par ultrasons afin de déterminer l’épaisseur de la matière. Ces systèmes de mesure sont simplement vissés dans le corps du palpeur et des rallonges en carbone peuvent être rajoutées si nécessaire selon la configuration de la pièce. Déporter le mécanisme de mesure vers le point de mesure, plutôt que le stylet, garantit le même niveau de précision quelles que soient les conditions de mesure.
Aucun équipement supplémentaire n’est nécessaire sur la machine. Quel que soit le système de mesure utilisé.
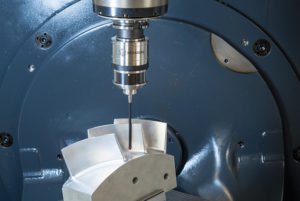
› Avec le RWP20.50-G-UTP, un palpeur à ultrasons est disponible pour la première fois en tant que standard industriel pour la mesure dans la machine-outil
Une nouvelle technologie de mesure dans la machine-outil : l’ultrason
Avec son système breveté de mesure par ultrasons dans la machine-outil, Hexagon ouvre de nouvelles voies dans la mesure automatique des épaisseurs de paroi. Le palpeur, dont la tête est équipée d’un capteur d’un diamètre de seulement 15 mm, plonge dans les poches de la pièce dans l’axe Z et entre en contact avec la paroi sur le point à mesurer.
Le capteur à ultrasons a préalablement été étalonné sur une pièce de référence. Une fois le palpeur placé sur la pièce, sa position est automatiquement lue et enregistrée. Puis les ondes ultrasonores sont émises au point de contact et se diffusent dans la pièce. Contrairement à la mesure ultrason manuelle, aucun fluide de contact n’est nécessaire pour déclencher le signal ultrasonore, comme c’est généralement le cas avec du gel ou de l’eau. Ainsi il n’y a pas de contamination de la pièce à usiner, et aucun nettoyage onéreux n’en découle.
Comme en optique, les ultrasons se réfléchissent sur la surface externe opposée de la pièce. Le cycle de mesure détermine le temps de réponse entre l’émission du signal et son retour. L’épaisseur réelle du matériau peut ainsi être déterminée avec une précision de seulement 10 µm. La valeur résultante est automatiquement transmise à la commande numérique avec les coordonnées de position et enregistrée avant que le palpeur ne soit déplacé vers le point de mesure suivant.
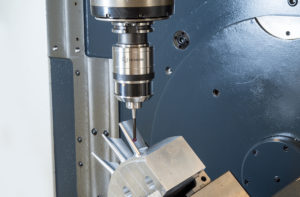
› Avec ce système de mesure à ultrasons, les industriels ont désormais la possibilité d’automatiser et de fiabiliser les contrôles manuels complexes
Une innovation brevetée
Un nombre quelconque de points peut être mesuré et enregistré dans le programme d’usinage sur la machine. Non seulement le gain de temps est énorme, mais aussi les résultats de mesure sont reproductibles à tout moment, intégralement et simultanément enregistrés et sans erreur. Ils peuvent être transférés vers des systèmes PPS et traités dans des bases de données, des tableurs et des logiciels statistiques. Ainsi, une correction ciblée des paramètres d’usinage est possible à tout moment, pour garantir le respect des tolérances en cours de production. Et en même temps, une documentation complète du suivi de production de la pièce est créée.
Avec le RWP20.50-G-UTP, un palpeur à ultrasons est disponible pour la première fois en tant que standard industriel pour la mesure dans la machine-outil. Il est installé dans le magasin d’outils et peut être appelé simplement par le programme d‘usinage. Comme les autres palpeurs Hexagon, le palpeur à ultrasons est essentiellement en acier inoxydable et étanche selon la norme IP68. Il est donc parfaitement adapté à l‘environnement difficile de la machine-outil. Tous les cycles nécessaires sont développés par Hexagon. Les CN Siemens 840D, Heidenhain TNC6x0 ou iTNC530 et Fanuc FAN sont disponibles. Ce palpeur communique avec le nouveau récepteur radio m&h RWR95.51 d’Hexagon. La tête de capteur UTP47.10 d’Hexagon convient à tous les matériaux métalliques et peut mesurer des épaisseurs de paroi de différentes dimensions.
Avec ce système de mesure à ultrasons, les industriels de l’aéronautique, notamment, ont désormais la possibilité d’automatiser et de fiabiliser les contrôles manuels complexes, souvent sujets aux erreurs d‘exécution. De plus, on fait plus confiance aux protocoles de mesure et aux certificats de qualité. Le retour des paramètres de correction dans le processus de fabrication peut être effectué pour chaque position et assurer la qualité de production des pièces suivantes.
EQUIP’PROD • N° 115 février 2020