Le recyclage « 4.0 » du fluide de coupe, une démarche simple pour d’importantes économies
BLASER SWISSLUBE / SCIE
parLa technologie 4.0 a du bon pour accomplir les tâches que l’on délaisse par routine, sans avoir conscience des économies à réaliser : plus besoin d’acheter un produit que l’on a déjà sous la main. La majeure partie du fluide de coupe consommé (huile ou soluble) est encore présente dans l’atelier : sur les copeaux, sur la pièce… Rien de plus simple que de réutiliser ce précieux liquide, après un processus de récupération et de traitement mécanique.
Spontanément, on pourrait être tenté d’utiliser le produit recyclé pour les machines les moins exigeantes : débit matières, usinage conventionnel… Une erreur, selon Blaser Swisslube, car il y a bien mieux à gagner. Certaines machines utilisent des process à forts débit ou pression d’arrosage et disposent de bacs de grande capacité (1 000 à 3 000 l.). De ce fait, les volumes de lubrifiant à récupérer sont conséquents. Il serait dommage de limiter le recyclage afin d’alimenter quelques machines équipées de bacs de 200 l., tout au plus.
Dès lors que le produit retrouve 100% de ses qualités originelles, le recyclage, même avec des moyens limités, devient une ressource financière de premier plan. L’enjeu est d’importance puisque les économies atteignent des sommets : « 30 à 70 % selon les dispositions et moyens mis en œuvre », annonce Blaser Swisslube qui encourage cette pratique écologique depuis plus de trente ans. Il n’est pas le seul à promouvoir le recyclage. Eric Chaboche, le gérant de S.C.I.E, constructeur d’installations de traitement automatisé de lubrifiants, explique, relevé en main, que « le volume des rajouts représente en moyenne 80% du volume d’huile annuellement consommée ». Avec une bonne organisation, la gestion du recyclage génère un gain rarement inférieur à 50 % des volumes précédemment achetés.
« Avec la récupération des égouttures, on peut déjà enclencher un processus de recyclage « simple » afin d’obtenir des résultats significatifs en combinant les opérations de filtration, de décantation et de déshuilage. »
Le recyclage, une opportunité pour faire de la qualité
Puisque la consommation et le coût de réassort sont très limités, l’utilisation d’un lubrifiant de qualité est à privilégier. En bénéficiant de la longévité du produit et de ses performances en usinage, on fait « d’une pierre deux coups ». Pour continuer dans cette démarche de qualité à « coûts = 0 euro », on s’applique à conserver les bacs à leur niveau maximum. Le cycle du lubrifiant est maintenu dans des conditions optimales de stabilité et de stress limité : taux de concentration et Ph stabilisés, dilution et filtration des impuretés, non saturation en huiles de graissage, régulation thermique améliorée…
En agissant sur l’environnement, on maintient la solution de lubrification à 100% de son potentiel : la productivité des process est fiabilisée et optimisée, la maintenance des machines et les besoins de vidange sont réduits. Le volume d’heures productives augmente, les coûts de destruction de produits usagés disparaissent. L’empreinte carbone diminue considérablement !
Plusieurs stratégies de gestion 4.0 du lubrifiant
« Il ne s’agit pas de faire du 4.0 pour redorer son image de marque », affirme Philippe Lacroix qui dirige la filiale française de Blaser Swisslube. Que l’on utilise 1 000 l ou 100 000 l. par an, la gestion 4.0 d’un lubrifiant offre de nombreux avantages. Elle peut se pratiquer à différents niveaux selon les objectifs de l’utilisateur : dans les machines pour le suivi des bains et une traçabilité au plus près des process, pour le pilotage d’une installation de recyclage ou d’une centrale de distribution. Avec ces solutions 4.0, tous les indicateurs sont connus, suivis et tracés : taux de concentration des bains, Ph, dureté de l’eau pour les solubles, viscosité dans le cas de l’huile entière ainsi que la température ou autre, si besoin est. Toutes les conditions sont donc réunies pour maintenir la fiabilité des process au plus haut de leur productivité. L’entreprise peut anticiper toute variation qui pourrait impacter la production, en agissant sur place ou à distance.
Partout des centrales 4.0
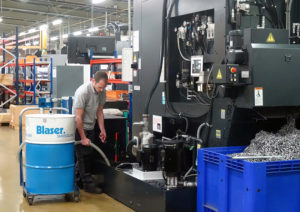
>> Pour une démarche qualité optimisée, le remplissage et le maintien au niveau maximum du bac machine chez Mecaprec
Elles sont déjà présentes dans certaines grandes structures et de plus en plus dans les PME. Principal équipementier du secteur, Eric Chaboche (S.C.I.E) surfe sur ce créneau voué à un fort développement. Facilement quantifiables, les économies réalisées permettent un retour rapide sur investissement, un argument qui fait mouche auprès des décideurs. « L’installation comprend un processus complet de recyclage avec ses bacs, ses procédés, ses capteurs et une automatisation intégrale du processus. Tout est sous contrôle numérique, il n’y a besoin de personne en interne pour le pilotage de l’installation, ce qui satisfait pleinement nos clients. »
Avant que le système de gestion automatisée du lubrifiant ne fonctionne, il faut calibrer le process, les équipements à intégrer et les systèmes de mesure qui composeront l’installation. Les besoins de l’entreprise, l’environnement de production et la nature du lubrifiant sont au centre du projet qui sera conduit dans un partenariat étroit entre l’utilisateur, le fabricant et formulateur du fluide de coupe et le fournisseur de l’installation. La technologie du lubrifiant est primordiale. Sa stabilité naturelle, en l’absence de conservateur, son adaptation au contexte de production et son suivi microbiologique relèvent d’une expertise très poussée du fournisseur. Celui-ci devra assurer l’analyse régulière des bains et la maintenance préventive dans le cas exceptionnel d’une dérive. L’utilisateur définit le taux de concentration de l’émulsion ainsi que les volumes à fournir.
Bien configurée, une installation de gestion automatisée comporte plusieurs bacs (arrivée des fluides usagés, traitements successifs, réserve de produit à distribuer) et différents paliers de sécurisation du process de recyclage. Une alimentation en dérivation avec 100% de produit « neuf » complète le dispositif d’une alimentation des machines totalement sécurisée.
Retour d’expérience pour Mecaprec Spécialisé dans la fabrication de pièces aéronautiques, de tout type de matière, l’atelier utilise Vasco 6000 de Blaser Swisslube, une huile soluble choisie pour ses performances et son adaptation à l’usinage des matières réfractaires. En décembre 2018, l’installation de gestion automatisée du lubrifiant est mise en route en présence des trois partenaires. Depuis cette date, le pilotage automatique gère la prise en charge des égouttures ou autres. Dès le bac d’entrée, des capteurs indiquent les mesures à prendre en compte pour la suite du processus. Toutes les phases s’enchaînent avec des contrôles de validation. Les appoints à très faible concentration permettent de retrouver le taux de concentration désiré. Des ajouts de « produit neuf » comblent le différentiel entre les besoins et les apports de produits usagés. L’écran installé sur le poste de pilotage renseigne le personnel chargé du suivi des bacs machines. Le responsable de production reçoit un reporting quotidien de toutes les données collectées, y compris la consommation en eau, le rendement… S.C.I.E, apporte la garantie d’une prise en main à distance avec une réactivité immédiate. D’une journée à l’autre, le taux de récupération par rapport aux besoins de l’atelier fluctue de 65 à 90 %. Le résultat consolidé sur un an dépasse 70 % des besoins annuels de Mecaprec. Un gain financier facilement chiffrable provenant de la baisse remarquable de consommation en eau et en lubrifiant auxquels s’ajoutent des dizaines de m3 de solution qui ne sont plus voués à la destruction. |
EQUIPPROD • N°122 Septembre 2020