Mise en pratique d’un mode de coupe ductile sur une machine Kern Micro HD
KERN Microtechnik
parDepuis mi-2021, la sous-traitance de Kern Microtechnik GmbH produit divers composants en céramique qui sont utilisés, par exemple, dans l’analyse. Le mode de coupe ductile développé par Kern joue ici un rôle important. Travaillant en étroite collaboration avec le client, les ingénieurs et techniciens de l’entreprise ont réussi à générer un processus stable qui se traduit par la plus haute qualité et un taux de rejet nul.
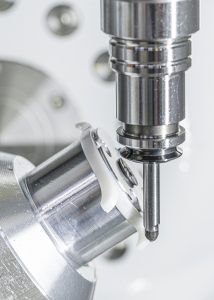
>> Ici, un boîtier de montre en oxyde de zirconium est fraisé sur un Kern Micro HD en cinq axes avec des outils PCD complets. (Photos : Kern Microtechnik).
Les entreprises des secteurs de l’analyse, de la chimie et des semi-conducteurs l’attendaient, tout comme les fabricants de composants de haute précision pour les machines de mesure, les montres/bijoux, la technologie satellitaire et bien plus encore. Nous parlons du traitement fiable des céramiques techniques telles que le carbure de silicium, les oxydes d’aluminium, etc. L’extrême dureté, la rigidité, la résistance thermique et chimique de ces matériaux et leur bonne conductivité thermique rendent les céramiques techniques intéressantes pour de nombreuses applications.
Cependant, leurs nombreux avantages posent un problème : le traitement est très exigeant. Aussi, parce que les produits en céramique doivent être fabriqués de manière irréprochable. Les fissures, l’écaillage et les dommages aux matériaux entraîneraient une défaillance des composants, car la propagation des fissures n’est pas inhibée – comme dans les métaux. De plus, les pièces doivent être fabriquées avec la plus grande précision dimensionnelle.
Le rodage et le meulage se sont avérés être des processus d’usinage traditionnels. Cependant, cela est associé à une restriction majeure dans la forme sélectionnable des composants. De plus, il existe une grande incertitude de processus dès que différents contours doivent être introduits. C’est exactement là qu’intervient le mode de coupe ductile développé par les ingénieurs de Kern, qui trouve de plus en plus sa place dans la pratique. Des outils de fraisage spéciaux avec une arête de coupe géométriquement définie permettent d’usiner les céramiques cassantes avec des copeaux de manière précise.
Usinage de la céramique avec une qualité stable
Alexander Stauder, responsable de la technologie d’application, explique que « dans la pratique, nous en tirons de nombreux avantages. La priorité absolue est la qualité nettement supérieure et stable du processus – en termes de précision d’usinage ainsi qu’en ce qui concerne la qualité de surface. »
De plus, il est souvent possible de réduire considérablement le temps de traitement, ce qui conduit finalement à une plus grande rentabilité. Cependant, il y a des limites. La règle d’or est la suivante : plus les pièces à usiner ou les alésages et rainures à réaliser sont grands, plus il est judicieux d’effectuer le premier enlèvement de matière plus important avec des meules peu coûteuses. Il ne reste alors que la finition importante pour le fraisage avec des outils coûteux, qui valent généralement plusieurs centaines d’euros. Plus les pièces ou les trous et rainures à réaliser sont petits, plus il est productif de fraiser directement avec le mode de coupe ductile.
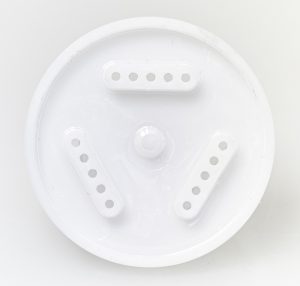
>> L’échantillon de pièce en oxyde de zirconium présenté a été entièrement produit par perçage et fraisage avec des outils PCD complets et un mode de coupe ductile.
Une machine extrêmement stable qui atteint les niveaux de précision les plus élevés est importante pour les deux processus. Une rigidité élevée et un fonctionnement dynamique et fluide, une broche à rotation rapide et une résistance à l’usure abrasive de la céramique sont des exigences de base pour l’usinage en mode de coupe ductile ainsi que pour la rectification de précision.
Diverses exigences pour le centre d’usinage
La Kern Micro HD est donc bien adaptée à ce type de traitement. Grâce à une astucieuse disposition des axes, la mécanique de ce centre de fraisage 5 axes haut de gamme est parfaitement protégée des poussières céramiques abrasives. La conception de la machine et l’hydrostatique à micro-écart unique garantissent une rigidité maximale. En combinaison avec la broche haute vitesse de 15 kW, qui atteint des vitesses allant jusqu’à 42 000 tr/min et est équipée d’une interface HSK 40, le centre d’usinage garantit un fonctionnement extrêmement silencieux et un enlèvement de matière économique.
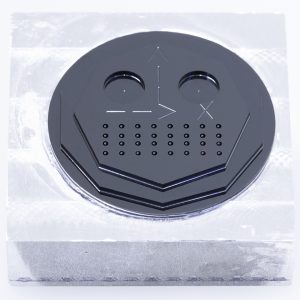
>> Le fraisage de la céramique avec le mode de coupe ductile développé par Kern est d’autant plus productif que les usinages à réaliser sont petits.
Conformément aux caractéristiques techniques, la Kern Micro HD maîtrise aussi parfaitement la rectification par coordonnées que le fraisage avec mode de coupe ductile. Si nécessaire, le meulage puis le fraisage final peuvent être effectués sans resserrage. Un avantage qui a un double effet positif en gagnant en temps et en précision.
Selon Alexander Stauder, d’autres facteurs sont également décisifs pour le succès dans la pratique. Outre le centre d’usinage 5 axes fiable et performant, la communication entre tous les acteurs figure en bonne place sur sa liste de priorité : « Personne ne connaît mieux le produit céramique à fabriquer et ses exigences que notre client, qui est souvent aussi le développeur. D’un autre côté, personne ne connaît la machine aussi bien que nous dans le domaine de la technologie d’application et de la fabrication en sous-traitance. Ces savoir-faire doivent s’unir. »
C’est précisément de cette manière que les premiers projets ont maintenant été mis en œuvre avec succès. Les proportions de meulage et de fraisage ductile sont très différentes. Étant donné que les composants et les tâches de traitement dans l’industrie de l’horlogerie et de la bijouterie sont toujours très petits, le fraisage est souvent effectué directement ici.
Exemple pratique : le taux de rejet atteint zéro
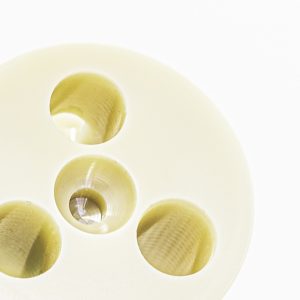
>> Ce composant en « oxyde de zirconium renforcé d’oxyde d’aluminium a été fabriqué sur une Kern Micro HD en un seul serrage grâce au fraisage et à la rectification par coordonnées avec un mode de coupe ductile.
Dans une commande en cours, Kern produit divers composants en céramique qui sont utilisés dans le monde de la métrologie. Ceux-ci étaient auparavant réalisés par un autre sous-traitant utilisant l’usinage par meulage. Alex Stauder raconte : « Comme nous l’a dit le client, l’un des principaux problèmes était que de petites imprécisions et les bords cassés les plus fins des pièces individuelles entraînaient à plusieurs reprises des défaillances dans l’assemblage. Nous avons pu éliminer complètement ce taux de rebut en passant par Kern. »
Ici, en huit étapes technologiques – de la poudre à la pièce finie – toutes les tâches de production sont réalisées à partir d’une seule source. Les deux dernières étapes de traitement sont effectuées sur le centre d’usinage Kern Micro HD. Les premiers débits d’enlèvement y sont effectués au moyen d’une rectification par coordonnées avec des pointes montées. Après cela – et c’est crucial – vient la finition avec le mode de coupe de fraisage ductile. Au cours de tests approfondis, l’équipe de technologie d’application de Kern a travaillé avec le client afin de déterminer l’épaisseur moyenne parfaite de la pièce nécessaire pour permettre à la pièce céramique de s’usiner correctement. « La fenêtre de processus étroite doit être maintenue de manière fiable, sinon la qualité des pièces en souffre et les outils coûteux sont soumis à un taux d’usure élevé », explique Alex Stauder.
Après avoir déterminé les paramètres de processus appropriés pour le traitement du matériau céramique utilisé, il était nécessaire de les réaliser avec une stabilité de processus de 100 %. Une tâche que la Kern Micro HD remplit parfaitement à Murnau. Le projet tourne depuis une bonne année. Les composants céramiques oxydes souhaités sont usinés de manière entièrement automatique 24h/24 et 7j/7 en série – sans déchets et avec une précision d’usinage inférieure à 2 µm.
EQUIP PROD • N°142 Mars 2023