Tous les regards sont tournés vers l’automatisation avec chaînage multiple
WFL
parCet article présente un projet unique tournant autour de l’automatisation centrale de quatre machines Millturn de WFL. Ce système clé en main présente toute une série de caractéristiques particulières. Le changement automatique des mâchoires, des pointes de la contre-pointe et des outils prismatiques, associé à un préhenseur à servomoteur permettant de couvrir une gamme de produits extrêmement large, permet un fonctionnement sans réglage des machines et de la solution d’automatisation.
Le système comprend un système de changement rapide de pinces entièrement automatique et un magasin de pinces. Des préhenseurs à servomoteur sont utilisés pour des pièces allant jusqu’à 250 kg. Des préhenseurs pour les outils prismatiques, les extrémités de la contre-pointe ainsi que les mâchoires intérieures et extérieures sont également utilisés.
Doté d’une charge utile de 480 kg, le robot à 6 axes est monté sur un 7e axe. Une gamme de pinces peut être ajoutée ou retirée du processus de production de manière entièrement automatique. Un bac de récupération intégré recueille quant à lui le liquide de refroidissement et les copeaux.
Postes de préparation et mesure des pièces
L’utilisation de deux stations de réglage pour les pièces et les outils permet de régler les outils puis de charger ou décharger de nouvelles pièces, parallèlement au temps d’usinage. Les deux diamètres auxquels les pinces tiennent la pièce sont déterminés par les deux pinces servo parallèles reposant sur un système de mesure de position. Ces deux valeurs sont comparées aux diamètres nominaux préalablement enregistrés.
Deux barrières lumineuses laser fixes déterminent la longueur des pièces et la comparent aux valeurs nominales de la recette. La valeur du décalage des pièces par rapport au point zéro du robot est également calculée.
Changement d’outil automatique, y compris le nettoyage et la lubrification
Un mandrin spécial permet un changement de mors entièrement automatique (remplacement simultané des jeux de trois pièces). Les pointes de la contre-pointe peuvent être changées automatiquement à l’aide d’une pince spéciale. Une autre pince spéciale est capable de changer automatiquement les outils prismatiques longs (jusqu’à 2 500 mm de long et 250 kg de poids).
Avant d’insérer le nouvel outil dans la machine, le robot se déplace vers une zone de nettoyage et de lubrification. Cela crée les conditions optimales pour un processus de transfert fiable.
En matière de contrôle, le système comporte trois niveaux de commande : une commande de robot Kuka KRC, une commande séquentielle Siemens PLC (technologie de sécurité) et une logique de cellule de l’ordinateur hôte et la gestion des recettes. Plus précisément, un ordinateur hôte de cellule gère les programmes CNC de manière centralisée et les met à la disposition de la machine. Des informations supplémentaires, telles que la gestion des outils et la planification des flux de matériaux, peuvent optimiser les temps d’utilisation de la machine, minimiser les temps d’arrêt et permettre également une production autonome.
Des avantages significatifs en matière de coûts et de flexibilité
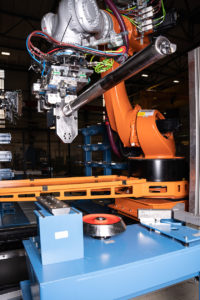
>> Poste de réglage de gauche à droite : pour les outils prismatiques, les pointes de la contre-pointe et les jeux de mors
Parmi les atouts de cette solution automatisée, le fonctionnement sans réglage via l’utilisation d’une pince servo flexible pour les pièces à usiner et d’une station de préhension à cinq positions.
L’entrepôt sert de « poumon » pour les vingt jeux de mors différents, les douze outils prismatiques différents, les six embouts de contre-pointe différents et les huit arbres différents (pièce non finie, pièce semi-finie, pièce finie). L’ordinateur hôte agit quant à lui comme un « cerveau » : il compile un programme de production optimisé sur la base des outils et des pièces disponibles de sorte que le système peut fonctionner de manière autonome pendant la nuit ou le week-end.
Autre avantage, la réduction des coûts unitaires, du fait par exemple d’une production sans personnel le week-end, d’un changement plus rapide des outils et des pièces et donc d’une meilleure utilisation des machines. En matière de flexibilité aussi, l’automatisation présente de sérieux atouts grâce à la pince universelle pour les pièces à usiner ; et du côté de la machine également grâce au magasin de mâchoires à vingt positions pour les différentes pièces de l’arbre, aux six différentes pointes de la contre-pointe et aux douze outils spéciaux du magasin. Enfin, le magasin d’outils central, le changeur d’outils spécial pour les outils lourds/longs, n’est nécessaire qu’une seule fois car la solution d’automatisation permet de couvrir toutes les machines. Des outils coûteux peuvent ainsi être utilisés sur les quatre machines, réduisant de fait les coûts des machines et des outils.
EQUIP PROD • N°131 Octobre 2021