Le contrôle au cœur de la réussite de Panerai
ZEISS / PANERAI / RUBIS CONTROL
parLa célèbre marque italienne de montres haut de gamme – entièrement fabriquées en Suisse – n’a cessé de renforcer son outil de production. Au-delà des machines d’usinage de pointe, la manufacture s’est également équipée de plusieurs machines MMT du constructeur Carl Zeiss, installées et mises en service par la société genevoise Rubis Control, spécialisée dans les prestations de mesure et partenaire de Zeiss depuis plusieurs années.
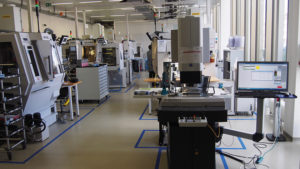
› Vue de l’atelier de production composé de centres d’usinage haut de gamme et de machines Zeiss pour du contrôle en production
Si la marque, bien connue des amateurs d’horlogerie haut de gamme, l’est moins du grand public en France, de l’autre côté des Alpes, en Italie, il s’agit d’une véritable institution. C’est en 1860 qu’une boutique dotée d’une école d’horlogerie voit le jour à Florence sous le nom d’Officine Panerai. A la veille de la seconde guerre mondiale, les premières montres furent créées pour les plongeurs de combat « Primo Gruppo Sommergibili ». Les montres Panerai et les instruments ont longtemps été réservés à la marine italienne avant que la maison soit rachetée par le groupe Vendôme (aujourd’hui Richemont) et s’ouvre au grand public. La marque fut placée sous la direction d’Angelo Bonati en 1997 ; ce dernier, sous l’impulsion du groupe Richemont, le géant du luxe déjà propriétaire de nombreux fabricants de renom, a fait redécoller une marque riche de toute cette histoire en lien avec la marine et la plongée.
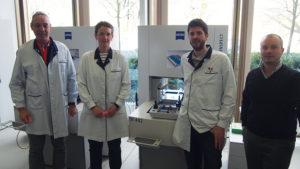
› De gauche à droite : Pascal Balouzat, Angélique Marguet, Nicolas Simon et Guy Hennard,
dans le laboratoire de métrologie composé de deux Zeiss O-Inspect 442
Pour ce faire, Panerai a dû gagner ses galons et devenir une manufacture au sens propre – et au sens suisse – du terme. En 2005, le premier calibre produit en interne sort des ateliers de la manufacture implantée au bord du lac de Neuchâtel. Dès lors, c’est une croissance à deux chiffres qui caractérise la marque, portée notamment par ses deux modèles emblématiques, la Radiomir (modèle datant de 1936 et dont le nom provient d’un brevet déposé en 1916 par Panerai et qui concernait une poudre rendant luminescents les cadrans d’instruments de visée) et la Luminor, collection apparue en 1949 et dont le nom s’inspire également d’une substance luminescente mais avec, en plus, un pont protège-couronne ; une caractéristique principale devenue icône.
Aujourd’hui, le très convoité label « Swiss Made » gravé sur la totalité des modèles témoigne d’une fabrication helvétique et d’un savoir-faire parfaitement maîtrisés en matière de haute horlogerie. « À l’horizon du projet de notre manufacture sur les hauts de Neuchâtel, nous avons développé une équipe industrielle tout en intégrant de nouveaux métiers, explique Guy Hennard, directeur industriel de l’entreprise. Panerai faisait appel à des prestataires pour certains composants. Mais à partir de 2014 nous étions désormais en mesure de tout produire en interne grâce à un outil de production de dernière génération, entièrement repensé, flexible et précis. Celui-ci nous a donné la possibilité de faire du milieu et du haut de gamme puis d’entrer dans la haute horlogerie en faisant de la qualité juste et du premier coup ».
Un concept d’usinage à part entière
Chez Panerai, la particularité de la manufacture, et plus spécifiquement celle de son processus d’usinage, est de sortir sans reprise une pièce taillée. Qu’il s’agisse de la platine, du pont ou des versions squelettes ainsi que de quelques pièces microscopiques, tout sort d’un seul tenant. La pièce est ensuite placée dans une navette en acier pour une opération d’ébavurage à l’eau (à 400 bar de pression !) et de microbillage à l’aide d’une poudre brevetée afin d’éviter les éventuels problèmes de qualité qui pourraient survenir aux étapes ultérieures de la production. « Ici, on contrôle chaque étape de la production. Seuls les essais finaux viennent attester du bon déroulement de la production ». L’objectif, on l’a compris, est de gagner un maximum de temps sur les opérations de contrôle et de traquer les moindres dysfonctionnements avant qu’il ne soit trop tard. Les pièces sont ensuite envoyées dans un tunnel de lavage avant de revenir pour une étape de gravage (au vernis bleu comme le veut la tradition chez Panerai), suivi du perlage de la platine et de la reprise des angles pour leur donner l’éclat le plus brillant possible. Enfin, on vient garnir la platine de goupilles, de pierres, de tenons et de pied-vis ; on y insère des rubis avec une précision de plus ou moins 5 microns.
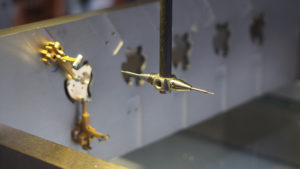
› Contrôle par palpage sur Zeiss O-Inspect avant d’envoyer les données de mesure vers le logiciel Calypso
Miser sur un outil de production haut de gamme
Pour la manufacture de Neuchâtel, la priorité n’est aujourd’hui plus à la croissance mais à la consolidation. Actuellement, le site recense pas moins de 400 équipements dont une quarantaine de machines-outils. « Les principaux défis de la production sont de deux ordres : faire face d’une part à un mix de produits avec des changements de série de plus en plus fréquents et des mises en train rapides. C’est un peu comme faire du prototype tous les jours de manière industrielle, fiable et économiquement pertinente, souligne Guy Hennard. D’autre part, notre principal défi est le micron : nous devons garantir à chaque cycle une capacité de mesure optimale car il s’agit de pièces à très forte valeur ajoutée. En somme, nous devons faire du micron du premier coup ». Chasser le micron et travailler chaque pièce comme un prototype industriel, c’est la priorité de Panerai, en particulier depuis les années où la manufacture a décidé d’internaliser toute sa fabrication d’ébauches du segment de haut de gamme. C’était aussi le moyen de répondre à de véritables problématiques industrielles et à la croissance de l’horlogerie d’une manière générale. « Lorsque que je suis arrivé dans le secteur, en 2011, j’étais étonné de voir que le contrôle était désolidarisé de la production, ce qui créait des goulots d’étranglement et des temps inutiles de mesure, se souvient Guy Hennard. Surtout, il devenait inconcevable d’aller chercher le micron avec des projecteurs de profil ou des instruments peu performants. Pour nous, il était devenu évident d’intégrer la qualité au cœur de nos métiers à travers de véritables moyens de mesure industriels et adaptés à la micro-mécanique aux cœurs des ateliers ».
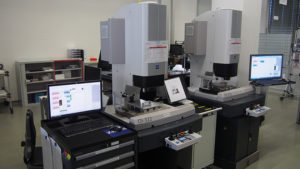
› Deux O-Inspect 322 situées au cœur de l’atelier d’usinage permettent de contrôler les éléments
de la montre en cours de production
Mais outre l’amélioration de la qualité, les acquisitions de moyens plus haut de gamme de mesure et de contrôle ont permis de responsabiliser les techniciens, à commencer par les régleurs. « Au départ, cela représentait un véritable changement de culture, ce qui n’était donc pas facile à faire accepter. Mais très vite, les collaborateurs ont vite compris ce que pouvaient apporter de tels moyens pour affiner leurs opérations de mesure ; aujourd’hui, à l’inverse, ce sont eux les demandeurs de machine de mesure tridimensionnelle ».

› À chaque étape de la production sa phase de contrôle, toujours sous l’œil aguerri des opérateurs
et des opératrices
La mesure et le contrôle au plus près de la production
Ces moyens de mesures ont fait leur apparition dans la manufacture dès 2012, au temps où l’ancien site de production se trouvait encore dans des locaux étriqués situés au bord du lac de Neuchâtel. Cette première machine, un Zeiss O-Inspect équipé d’optique et de palpeur, était destinée au contrôle d’entrée pour la soumission des pièces venues de l’extérieur ou pour du contrôle afin de mesurer la planéité et la hauteur des composants. Aujourd’hui, dans ce nouveau bâtiment de 10 000 m² sorti de terre en 2014 et surplombant la ville de Neuchâtel, pas moins de huit machines de mesure tridimensionnelle (MMT) Zeiss (six en production et deux dans le laboratoire de métrologie) accompagnent la montée en puissance, en qualité et en fiabilité d’une manufacture qui n’a cessé de se réinventer tout en gardant l’esprit d’origine des montres initialement dédiées à la Marine Royale Italienne.
EQUIP’PROD • N° 110 mai 2019