Les solutions de m&h permettent à Mitec d’économiser 50% de travail manuel
M&H / MITEC MIKROTECHNOLOGIE
parPetit et fin… Telle est la devise de la société allemande East Mitec spécialisée dans la mécanique de précision. Les moules et les outils utilisés pour la fabrication de pièces de grande finesse et de composants avec microstructures sont vérifiés alors que les pièces sont encore bridées dans la machine. Cette vérification s’opère selon une tolérance définie grâce au matériel et au logiciel de la gamme m&h d’Hexagon. Cela permet d’économiser 50% du travail manuel.
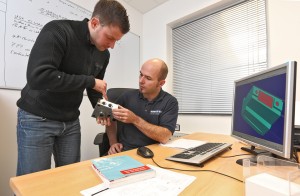
Maik Harbich, directeur général de MITEC, est plus que satisfait des palpeurs m&h et du logiciel 3D Form Inspect
Les pièces particulièrement fines de l’industrie optique, l’ingénierie médicale ou la technologie des capteurs et du fluide proviennent de moules et d’outils fabriqués par Mitec Mikrotechnologie GmbH à Limbach-Oberfrohna dans le Vogtland. La jeune entreprise, fondée en 2008 seulement, s’est déjà forgé une excellente réputation pour la fabrication de pièces de précision dans ces secteurs d’activité.
Implantée sur un site vierge, la société est entièrement orientée vers la fabrication à haute précision des structures les plus fines. Un sas à l’intérieur du site de production permet de maintenir des conditions ambiantes pratiquement propres. Le parc machines comprenant des machines Huron et Makino est installé dans des ateliers à température contrôlée assurant des conditions d’usinage constantes. Le centre d’usinage Makino est équipé à la fois du refroidissement de broche et de glissières et vis-à-billes refroidies – une condition importante pour la fabrication de pièces précises avec de petites géométries et des tolérances de ±2,5µm. Dans les fluides, il existe souvent des structures capillaires avec des conduits de seulement 50 x 50 µm. Les électrodes correspondantes sont usinées en graphite avec des dimensions de 30 x 30 µm. Pour l’usinage dur, ils travaillent en UGV en utilisant des fraises pouvant descendre jusqu’à 0,1 mm de diamètre.
Des avantages en matière de précision et de rentabilité
La machine Huron VX6 avec commande numérique Siemens 840D est utilisée pour l’usinage d’ébauches. La Makino V33 et la Makino 5 axes V22, toutes à commande Fanuc, sont exclusivement utilisées pour la finition et l’usinage fin. Le VX6 Huron est équipé d’une combinaison de palpeurs Hexagon comprenant le palpeur pièce m&h IRP32.00 et le palpeur outil IRT35.70. Ces deux appareils communiquent avec la commande numérique par transmission infrarouge avec le même récepteur. Les longueurs et les diamètres réels d’outils sont mesurés avec le palpeur-outil et enregistrées comme valeurs de correction dans la commande numérique. Cela permet un travail précis, en prenant en considération la situation de serrage respective des outils. Comme ce sont surtout des outils de grand diamètre qui sont principalement utilisés dans la machine, le palpeur-outil m&h IRT35.70 avec son grand disque de palpage est à la fois adapté et rentable. Le centre 3 axes Makino V33 est également équipé d’un palpeur pièce m&h IRP32.00.
Pour l’orientation pièce, les arêtes sont déterminées avec le palpeur, ce qui réduit le temps machine dédié normalement au positionnement. Dès que les pièces ont été usinées, les contours sont mesurés à des points critiques en utilisant le logiciel m&h 3D Form Inspect et une comparaison nominale / réelle est faite par rapport au dessin CAO. Cela permet de surveiller de près l’usure des outils et l’opérateur sait immédiatement si oui ou non il a besoin de faire des ajustements. Les écarts résultants des outils lors de l’usinage peuvent être détectés à un stade précoce. En cas de problème, une reprise mécanique est faite alors que la pièce est encore bridée dans la machine. Cela permet de maintenir des tolérances serrées et évite les reprises chronophages.
Sur la Makino V33, la mesure de la pièce encore dans la machine est maintenant une partie intégrante du cycle d’usinage chez Mitec. Même pendant la mise en place de la pièce, ou quand ils s’aperçoivent parfois d’une déformation due à un durcissement, le m&h 3D Form Inspect est utilisé pour valider. A cet effet, c’est le module logiciel Best Fit dont on se sert. Celui-ci trouve la position de la pièce à usiner à partir de ses principaux contours et transmet les valeurs de correction à la commande numérique. La CN déplace alors les points 0 en conséquence et ajuste la position du programme d’usinage à la position réelle de la pièce. Cela signifie que la pièce n’a besoin d’être fixée qu’à peu près dans la position voulue. Avec cette procédure, non seulement la mise en place de la pièce est raccourcie, mais son usinage est optimisé en supprimant les « fraisages dans le vide », qui étaient assez fréquents si une déformation importante avait eu lieu. En particulier pour les fabrications de moules, utilisant plusieurs plaques dont les contours 3D s’imbriquent, cet alignement électronique avec le 3D Form Inspect et Best Fit est une aide indispensable.
Maik Harbich, le responsable du fraisage chez Mitec, est enthousiaste en décrivant son expérience avec le m&h 3D Form Inspect: « Pour les facettes de moule et les transitions tangentielles, qui doivent avoir certains rayons vérifiables, le 3D Form Inspect est tout simplement indispensable. » À titre d’exemple, il se réfère à un outil de pliage qui a été construit en utilisant plusieurs plaques, qui montraient ces transitions dans le contour. Sur l’outil, une tolérance de seulement +/- 5μm était définie. Les inserts ont été usinés en semi-finition avec un écart de 0,02 – 0,03 mm. Ils ont été mesurés avec le m&h 3D Form Inspect puis finis selon les résultats mesurés. « Tout marchait parfaitement, ajoute Maik Harbich. Il n’y avait même pas besoin de retoucher ! »
- Une électrode en graphite avec beaucoup de transitions 3D et des structures internes est contrôlée dans la machine en utilisant les produits m&h.
Un avantage concurrentiel certain
Dans un autre cas, un moule d’injection a été fabriqué, également sans retouches. « Lors de l’échantillonnage du moule, nous pouvions complètement le sceller en augmentant simplement la pression de contact », rapporte Maik Harbich avec fierté. Après l’introduction du logiciel de mesure sur la machine, les cycles de fabrication à Mitec ont été considérablement raccourcis. « Nous avons réduit le travail manuel ultérieur d’un bon 50%. Cela donne à l’entreprise un avantage concurrentiel certain ». Maik Harbich décrit ainsi les réalités auxquelles il fait face : « Les clients ont de plus en plus besoin de délais courts. Aujourd’hui, le temps entre la réception du projet et l’outil fini est très court. » Les logiciels et palpeurs m&h d’Hexagon ont été très utiles à cet égard. Surtout la manipulation simple et la possibilité d’une programmation facile dans l’atelier sur la machine sont louées par Mitec.
« Nous avons rapidement clarifié les premières questions sur les manipulations avec le service Hexagon, explique Maik Harbich. Après le premier étalonnage et le réglage des paramètres de la machine par Makino tout s’est exécuté sans problème ».
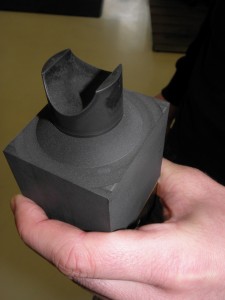
Ce contour 3D de graphite a été vérifié, encore bridé dans la machine, en utilisant le logiciel m&h 3D Form Inspect.
Naturellement, au premier test, Mitec a d’abord fait une comparaison avec les résultats de leur machine de mesure. Ce sont des outils pour les fluides particulièrement critiques avec des géométries étagées et des tolérances très serrées qui ont été utilisés comme validation. Les écarts détectés étaient de quelques microns avec une déviation maximale d’environ 8 μm. « Les contours 3D doivent tout simplement être corrects. Pour vérifier cela, nous avons besoin du m&h 3D Form Inspect. Cela sécurise les opérateurs machines et nous savons à un stade précoce que nos pièces sont précises et conviendront ». Voilà pourquoi c’est seulement une question de temps avant que le Makino 5 axes V22 soit également équipé de palpeurs m&h.
Karl-Heinz Gies
N° 80 Septembre 2016