Figeac Aero réduit de moitié le coût de certaines opérations d’ébauche avec les fraises ASPX Diaedge
MMC METAL FRANCE / FIGEAC AERO
parDans un contexte conjoncturel difficile, où la priorité du secteur aéronautique réside aujourd’hui dans la réduction des coûts de production, Figeac Aero, sous-traitant de rang 1 bien connu des avionneurs, est parvenu à diminuer de moitié le coût d’usinage de certaines opérations d’ébauche de ses pièces de structure en métaux durs grâce à un développement spécifique mené avec Mitsubishi sur les fraises hérisson ASPX.
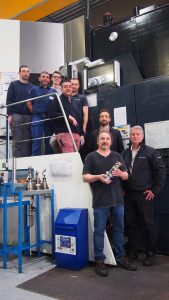
>> De haut en bas et de gauche à droite :
Bastien Tetuan (leader technique process), Édouard Nouira (chef d’équipe usinage), Damien Grandet (chef de projets techniques), Ludovic Bruel (responsable Industrialisations Métaux Durs), Yohan Pouget (responsable process métaux durs), Grégory Lafon (ingénieur d’application MMC Metal France), Freddy Couderc (expert outil coupant) et Laurent Le Méteil (responsable Business Aéronautique MMC Metal France)
C’est un projet qui a pris plusieurs années. Dans la petite ville de Figeac (Lot), haut lieu de l’industrie aéronautique, les centaines de salariés du site opèrent dans les différents ateliers de production : aluminium, pièces moteur et précision, assemblage, métaux durs ; dans ce dernier département entièrement dédié à la production de pièces de structure d’avion en titane et en inconel, travaillent en 3-8 environ 90 personnes pour le compte de Figeac Aero et ont regagné les constructeurs d’avions.
L’unité Métaux durs réalise environ 2,2 millions d’euros mensuels de chiffre d’affaires effectués sur environ 7 000 heures de travail. Sa fonction ? Produire pour les avionneurs des pièces de structure telles que des longerons, des nervures, des ferrures et des attaches-moteur. « Pour ce faire, notre atelier abrite huit machines de grande dimension pour des pièces atteignant jusque 4 mètres de longueur, et une trentaine de machines de moyenne dimension nous permettant d’usiner des pièces jusqu’à 1 mètre 50 », précise Yohan Pouget, responsable process Métaux durs Figeac Aero. En poste depuis trois ans, celui-ci a récupéré un projet majeur dans cette unité de production visant à mettre en place une nouvelle fraise hérisson dotée de performances permettant de réduire encore considérablement les coûts d’usinage.
Le besoin de renouveler la technologie en matière d’ébauche
En février 2018, l’usine tourne à plein. Les carnets de commandes sont remplis et les machines tournent en continu, en 3-8, y compris le week-end. Dans ce contexte, les unités de production n’avaient qu’une priorité : « aller toujours plus vite en faisant moins cher », rappelle Yohan Pouget. Or, les fraises utilisées dans les machines pour l’ébauche de pièces, en lieu et place dans les machines depuis une dizaine d’années, semblaient avoir fait leur temps. « En dix ans, les technologies évoluent fortement et rapidement dans le domaine de l’usinage, rappelle Laurent Le Méteil, Business Aerospace Manager MMC Metal France, en charge de répondre à l’appel d’offres lancé par Figeac Aero il y a un peu plus de quatre ans. La technologie de fraises hérisson VFX de Mitsubishi Materials utilisée jusqu’alors, avec ses plaquettes aux 2 arêtes de coupe, pouvait être mise en concurrence avec du fraisage monobloc ou de la grande avance si le débit copeaux était en second plan ».
Certes, depuis le démarrage du projet en 2018, la crise du Covid-19 est passée par là, emportant avec elle les rêves de croissance de l’industrie aéronautique, en brisant de façon brutale le dynamisme de toute une filière. Le « produire plus vite » a donc été mis de côté pour laisser la place au « produire moins cher ». Une stratégie vitale pour Figeac Aero qui, comme tant de sous-traitants de rang 1, a subi de plein fouet la crise des long-courriers. « Mais si la crise a retardé le projet, cela ne nous a pas empêché d’avancer. Et après avoir réalisé une étude de marché et mis en concurrence différents fabricants d’outils coupants, notre choix s’est rapidement orienté vers Mitsubishi Materials et une nouvelle technologie de fraise hérisson que nous avons développée ensemble. »
Une solution d’ébauche pensée pour l’aéronautique
Lorsque Ludovic Bruel, ancien responsable outils coupants de l’unité Métaux Durs, a lancé l’appel d’offres auprès des différents carburiers, Mitsubishi Materials s’engageait en parallèle dans le développement d’une nouvelle fraise hérisson auprès de trois grands clients en France et un en Grande-Bretagne. Parmi eux figuraient notamment le sous-traitant Mecaprec (implanté à Lavelanet, dans l’Ariège) et… Figeac Aero. « Le département R&D du siège de Mitsubishi Materials situé au Japon nous a sollicités pour effectuer des tests de ce projet de fraise baptisée ASPX car c’est en France que sont le plus souvent utilisées les fraises de ce type en raison de la forte présence de l’aéronautique sur notre territoire, confirme Laurent Le Méteil. Pour ce faire, nous avons retenu trois sites industriels et celui de Figeac en faisait partie. Après avoir présenté notre projet, nous avons pu démarrer les essais à la fois au Cetim mais également chez Figeac Aero afin de vérifier les forces, la vitesse, les puissances absorbées, la répétabilité et la durée de vie ».
De son côté, Freddy Couderc, Expert Outils coupants au sein de l’unité Métaux durs de Figeac Aero et acteur à part entière du projet, précise avoir eu recours à la « méthode sur éprouvette afin de déterminer les puissances absorbées et générer des courbes d’usure avant de passer à des tests grandeur réelle ; un moyen de mesurer en temps réel les efforts sur la pièce et de constater si les résultats concordaient bien avec ceux de Mitsubishi Materials ».
Et les résultats étaient au rendez-vous. Les efforts générés sur l’axe ont permis de réduire de façon significative les sollicitations sur la broche tout en maintenant un niveau de qualité d’usinage optimal. Par ailleurs, la fraise ASPX a permis de sécuriser le process : si les anciennes générations d’outils provoquaient parfois des casses, ce n’est plus le cas aujourd’hui en raison de la réduction d’efforts sur la broche. Mais c’est au niveau des coûts que les résultats ont été les plus impressionnants : « avec la nouvelle fraise hérisson ASPX, nous avons divisé par deux les coûts de production en obtenant plus précisément des gains de 48 % ! », confirme Yohan Pouget.
Une technologie avancée associée à un accompagnement sur mesure
Destinée à l’ébauche à haut rendement, la fraise hérisson ASPX, associée à ses plaquettes à 4 arêtes de coupe, a ainsi séduit Figeac Aero pour différentes raisons : « cette fraise est capable de rainurer dans le titane avec un fort débit copeaux – près de 500 cm3 par minute avec une profondeur et une largeur de passe de 80 mm et une vitesse de coupe de 50 m », précise Laurent Le Méteil. Grégory Lafon, ingénieur d’applications MMC Metal France, spécialisé dans l’aéronautique, ajoute que cette fraise à cinq « est résolument un produit inédit, intégrant de nouvelles géométries de plaquettes, une nuance – la MP9140 – plus tenace, développée à l’origine pour les matériaux réfractaires mais pouvant s’appliquer à bien d’autres matières ».
Cependant, pour Mitsubishi Materials, d’autres défis étaient à relever. Il ne fallait en aucun cas bouleverser la production ; « il était important de remplacer, sans reprogrammation, la VFX par l’ASPX ». Un défi relevé grâce à une collaboration entre Yohan Pouget et Freddy Couderc avec l’équipe française de Mitsubishi Materials, composée de Laurent Le Méteil et Grégory Lafon, qui précise également « avoir reçu un soutien très important du Japon. D’ailleurs, Yamazaki Kiichi, le concepteur de la fraise ASPX, et Takayuki Azegami, le coordinateur technique aéronautique au niveau européen, sont venus sur place et nous ont beaucoup épaulé dans ce projet ». Un accompagnement très apprécié chez Figeac Aero : « les équipes de Mitsubishi Materials étaient toujours là quand on avait eu besoin de conseils. Il y a eu beaucoup de présentations et de discussions sur nos attentes, ce qui a d’ailleurs grandement fait évoluer le produit ».
Déployée dans le bâtiment B10, la fraise hérisson ASPX Diaedge de Mitsubishi Materials va également intégrer les machines du B6 dans les deux années à venir. De quoi pouvoir absorber de nouvelles commandes, notamment au niveau des vols longs courriers. Dans tous les cas, chez Figeac Aero, on se dit « résolument prêts » à relever les défis que posera le rebond tant attendu de l’aéronautique.
EQUIP PROD • N°139 Octobre 2022